CASE STUDIES

LABEL VERIFICATION RED, BLUE OR GLUE?
Business Problem
Operators are sometimes given the wrong or mixed stacks of pre-printed labels as well as not ensuring the label feeder has been cleared of the previous production runs labels. Any one of these presents the manufacturer with the potential of pallets full of mislabeled product leaving the facility costing time and money in rework and charge backs from the supply chain.
Solution
A UPC barcode inspection system was added to each production lines roll through labeling systems. The operators, using a hand scanner are now required to scan the UPC barcode on the pre-printed label stack. Information from this UPC scan is then used to set the match code value for the fixed mount barcode readers on the production line.
As product travels down the line. The fixed mount barcode readers scan each applied label. In the event a UPC is read that does not match, a red light with audible alarm are enabled and the product is rejected from the line. In the event that three or more consecutive mismatch scans occur the line is stopped by the system using discrete I/O.
Result
With a minimal investment the customer was able to stop the mislabeling of product before filling. This saved thousands of dollars in rework and product return costs. This system paid for itself in weeks.
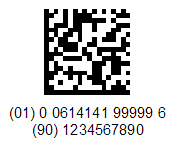
LABEL AND CASE
CODE VERIFICATION SHRIMP OR CHICKEN?
Business Problem
A food manufacturer had no control over the labeling process. Two pre-printed labels were applied to each container after filling. Operators were occasionally placing the wrong rolls of labels onto the label applicator as well as the supplier of those labels splicing rolls of mismatched labels together. For this manufacturer in the food industry, rework was the least damaging outcome. Many of the products produced contained allergens which could negatively affect the consumer, exposing the manufacturer to potential law suits as well as costing time and money in rework and charge backs from the supply chain.
Solution
A complete identification system with custom software, induct and verification scanning as well as PLC control was implemented. Operators are now required to login to the system, select the item from a database, and scan both of the product labels to ensure the line is correctly setup.
As product travels down the line the fixed mount barcode readers scan each containers applied 2D barcode labels. In addition, once the product is in the case, the case code is scanned to be certain the correct case label has been applied. In the event a products label or case code is not read, the product is rejected off the line. If a mismatch is found the line is stopped and alarms activated.
Result
Within one month of installation the system had twice stopped mislabeled product from leaving the building. There was an immediate return on investment for the customer who then expanded the system to all production lines.

CASE LABELING...
TO LABEL OR NOT
TO LABEL?
Business Problem
A contract food manufacturer serving multiple customers had a case labeling challenge. Some of its customers provided corrugate cases already printed with case codes and some did not. The challenge was that all cases ran down the same conveyor line with unmarked cases needing a case label and previously printed case needing to pass through.
Solution
A pre-printed corner wrap label applicator and induct scanner were added to the line. As cases traveled down the conveyor the induct scanner would trigger and look for the cases barcode. If the case code was scanned, the system would pass the case down the line. If no case code was scanned. The label applicator would trigger and apply a case label onto the case.
A complete identification system with custom software, induct and verification scanning as well as PLC control was implemented. Operators are now required to login to the system, select the item from a database, and scan both of the product labels to ensure the line is correctly setup.
As product travels down the line the fixed mount barcode readers scan each containers applied 2D barcode labels. In addition, once the product is in the case, the case code is canned to be certain the correct case label has been applied. In the event a products label or case code is not read the product is rejected off the line. If a mismatch is found the line is stopped and alarms activated.
Result
The customer was able to identify each case produced without having to incur the costs and disruption of having to expand the conveying system. The resulting increase in utilization of the line, no lost floor space and a simple to use system solved a significant challenge for the manufacturer.
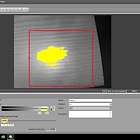.png)
COVERT CASE MARKING...
WHAT'S IN THE CASE?
Business Problem
A manufacturer of plastic components had the need to identify items originating from multiple mold machines, all in the same generic case and all merged onto the same case labeling line. Several issues had to be overcome.
-
The marketing group refused to allow any marking to the case other than the primary case label.
-
The cost of placing 14 label printer applicators in the system along with space required.
-
Layout of the plant floor and various operational factors were a challenge.
Solution
A complete turn-key system with custom software, inkjet pens, label printer-applicator, and camera inspection were provided. Prior to starting production the item running on each mold machine is setup. As each case exits the mold machine an inkjet pen applies a UV ink mark onto the side of the case and identifies the mold machine the case originated from. All cases are then merged into a single line for case labeling. As each case approaches the label printer-applicator a UV light and Cognex camera inspect the case. At this point the UV mark will fluoresce and depending on the marks position on the case, determine which mold machine it originated from. The system software then selects and sends the correct case label for the item to the printer-applicator. After application both a barcode scanner and camera inspect and verify that the correct label has been applied to the case.
Result
The marketing group couldn’t see anything other than the label on the case! Huge win with that alone. The system cost, complexity, and floor space required were all kept to a minimum by utilizing UV ink and the produced product is accurately identified